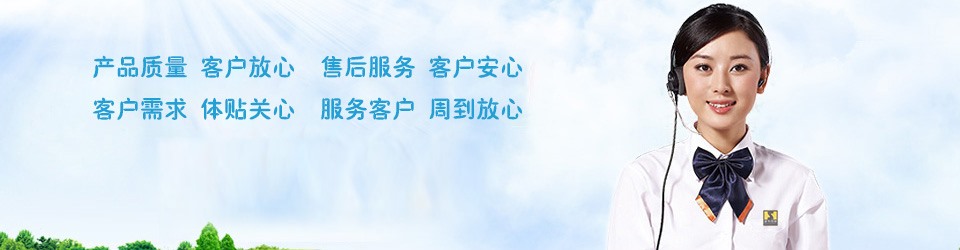
挤出复合薄膜剥离强度影响因素浅析
发布时间:06-30 作者:小华 来源:深华印材 查看: 次
挤出复合薄膜剥离强度影响因素浅析
挤出复合工艺具有投资少、成本低、生产效率高、操作简便等多方面的优点,因此,它在塑料薄膜的复合加工中占有相当重要的地位。但是,在实际生产中也难免会出现这样或那样的问题。本文,就以最为常见的剥离强度差为例与大家共同进行分析探讨。
一、薄膜基材对剥离强度的影响
1、基材表面处理效果对剥离强度的影响。被涂布基材应当预先进行电晕处理,电晕处理后的表面张力应当达到40达因以上,这样可以改进基材同熔融挤出树脂的粘结性,从而提高挤出复合强度。因此,在生产前要检测基材的表面张力是否达到要求,一发现表面张力太低,应立即更换基材或对基材重新进行表面处理。此外,经表面处理过的薄膜,其表面张力应当是均匀一致的,否则也会对剥离强度产生一定的影响,造成剥离强度不均匀、不一致的问题。
2、基材表面清洁度对剥离强度的影响。被涂布基材表面应当清洁、干净,无灰尘、无油污,如果基材表面不太清洁,粘附了灰尘、油脂等污物,就会直接影响到熔融树脂跟塑料薄膜表面的粘合力,从而使挤出复合膜的粘接强度下降。
3、其它因素的影响。对于一些易吸湿的薄膜材料(比如尼龙薄膜),如果已经发生吸湿现象,这也会影响挤出复合膜的粘接牢度。因此,对于易吸湿的薄膜材料一定要注意防潮,尼龙薄膜在使用前和使用后应当及时用铝箔将其包裹好。
二、油墨对剥离强度的影响
1、油墨质量对剥离强度的影响。
在实际生产过程中,有时候会出现无油墨或油墨较少部位的剥离强度好、而有油墨或油墨较多部位的粘合牢度反而比较差的现象,这就是由于所用的印刷油墨的适性不好,油墨与基材之间的粘接不良,从而造成挤出复合膜的剥离强度差。一旦发生这种情况,应当及时更换合适的油墨,并同油墨厂商联系,共同协商和研究解决办法。
2、油墨干燥性对剥离强度的影响。如果油墨干燥不良,特别是当油墨中大量地使用了甲苯、丁醇等沸点比较高的溶剂,而且干燥箱温度设置
不当的话,就会有少量或较大量的溶剂残留在油墨层中,复合后可能会造成复合膜的分层,使剥离强度变差。因此,在印刷过程中一定要对油墨的干燥性能进行严格的控制,保证油墨能够充分干燥。
此外,在印刷过程中还要注意对印刷速度和干燥温度等工艺条件的控制,因为它们也会对油墨中溶剂的挥发速度产生一定的影响。如果印刷速度较快,且印刷机干燥箱的温度又比较低的话,油墨中的溶剂可能无法完全挥发掉,这些残留的溶剂就会在薄膜上形成一些小泡,使复合膜粘接牢度下降。一般来说,在设定干燥箱的温度时,必须要综合考虑印刷速度、油墨的干燥速度、承印物材料的种类以及印刷图像的大小等因素。
三、挤出复合用树脂对剥离强度的影响
1、树脂类型对剥离强度的影响。挤出涂布复合用树脂可以是聚乙烯、聚丙烯、EVA、Surlyn、 Nucler、Bynel、EVAL、EAA、EMAM等。挤出涂布复合的目的不同,选用的树脂也不同。例如,用于普通层复合塑料制袋用的,可以采用热封性较好的各种热封用树脂;用于夹心挤复用的树脂,要求同面层和内封层塑料层均有良好的相容性的,可根据面层及内封层材料的不同选用各种相容剂树脂,如 Surlyn、Nucler、Bynelr等。如果树脂选用不当,会影响到它同被涂布基材的相容性,从而影响到挤出复合强度。
2、树脂熔融指数(MI)对剥离强度的影响。熔融指数(MI)是指树脂熔融料在一定温度和一定压力下,在lOmin内通过标准毛细管的重量值,以克/1Omin表示。熔融指数(MI)是树脂流动性的一种指标,一般来说,树脂的熔融指数(MI)越高,则其流动性越好,熔融薄膜的粘度越低,粘合力越大。在挤出复合工艺中,不宜选用熔融指数(MI)太小的树脂。如果树脂的熔融指数(MI)偏小,其分子量较大,则融合性比较差,不能与被涂布基材很好地粘合,致使剥离牢度有所下降。比如在使用LDPE树脂进行挤出复合时,一般选用熔融指数(MI)在4--7g/1Omin的LDPE树脂。
3、树脂密度对剥离强度的影响。树脂的密度越小,支链含量越高,表面越容易被活化,粘合力就越大,对剥离强度的提高也就越有利。
4、树脂中助剂及水分含量对剥离强度的影响。树脂中的助剂,特别是润滑剂对挤出复合膜的剥离强度有着很大的影响,比如在使用LDPE树脂进行挤出复合时,应当选用不含或少含润滑剂的挤出涂覆级树脂粒子,例如北京燕山石化公司的1C7A、上海金山石化公司的1C8A等树脂。此外,如果树脂中所含的水分比较多的话,在挤出复合过程中可能会发生塑化不良现象,从而影响复合膜的剥离强度。
四、挤出复合工艺对剥离强度的影响
1、挤出机温度对剥离强度的影响。挤出机机筒温度和T模温度的控制极为重要,是挤出复合工艺的关键和核心。温度太低,树脂塑化不良,从模口流延下来不能很好地与基材复合,致使剥离牢度下降;温度高,流出的熔薄膜氧化越充分,表面产生极性分子,对基材的亲和力越大,剥离强度也就越高。但是温度也不宜过高,否则树脂容易分解,还可能会烫伤基材,而且还会产生烟雾,污染工作环境。一般来说,挤出机机筒的温度通常控制在150℃一340℃之间,T模的温度通常控制在310℃--340'C左右,这还要根据挤出复合设备和所用树脂的具体情况来设定。
2、树脂温度对剥离强度的影响。树脂温度高,有利于熔融塑料膜在被涂布基材上的润湿和渗透,因而有利于复合强度的提高,但过高会引起分解,一般不超过350℃。如果树脂与基材压着时的温度过低,树脂表面氧化不充分,应当适当提高树脂温度。
3、气隙对剥离强度的影响。气隙是指从挤出模口到复合冷却钢辊、压力辊接触线之间的距离。由于气隙的存在,热熔膜表面会同空气中的氧气发生氧化作用,氧化后的热熔膜被涂布塑料薄膜复合时的剥离牢度会大大提高。气隙的大小对挤出剥离强度也有很大的影响,气隙太小,树脂表面氧化不充分,致使挤出复合强度变差;气隙大,热熔膜同空气接触的时间长,热熔膜表面被空气中氧气氧化的程度越厉害。增加极性基因,树脂同基材表面的黏结力也就越大,从而有利于复合强度的提高。但如果气隙太大,则热熔膜的热损失过大,温度会降低得过多,在复合时的温度过低,反而会引起剥离强度的下降,而且热封性也变差。因此,挤出复合时应当根据实际情况来调节气隙的大小,一般来说,气隙控制在 50mm—l00mm之间为宜。
4、复合压力对剥离强度的影响。复合压力小,熔融树脂与基材之间贴合不紧密,会使剥离牢度下降。但复合压力也不可太大,否则基材容易被压变形。
5、冷却钢辊表面温度对剥离强度的影响。冷却辊采用的是表面镀铬的钢辊筒,其作用是将熔融树脂薄膜的热量带走,让粘合后的复合膜立即冷却、固化,以形成较强的内聚力,使熔融薄膜跟被涂布基材粘牢、定型,不产生相对位移,从而保证良好的剥离强度。因此,冷却钢辊表面的温度对挤出复合薄膜的剥离强度有着一定的影响。如果冷却钢辊的表面温度太高,则冷却定型效果不好,可能使挤出复合膜起皱,会使复合牢度下降;但如果冷却钢辊的表面温度太低,冷却速度太快的话,也会引起复合强度的降低。一般来说,冷却辊的表面温度控制在30'C左右最佳。而且,冷却辊表面必须光滑,表面温度分布应当均匀一致,这样才能保证挤出复合膜的冷却效果一致,从而保证其粘接牢度和剥离强度的一致性。
6、硅橡胶压力辊表面状态对剥离强度的影响。硅橡胶压力辊的作用是将基材和熔融树脂膜以一定的压力压向冷却辊,使基材和熔融膜压紧、粘合,并冷却、固化成型。硅橡胶压力辊是在钢辊的外表面包覆了20—25mm厚的硅橡胶而制成的,硅橡胶的硬度一般为80--85肖氏硬度为最佳,而且,硅橡胶压力辊表面的硬度应当均匀一致,这样才能保证整体压力基本保持均匀一致,从而保证挤出复合产品剥离牢度的均匀、恒定。
7、复合线速度对剥离强度的影响。在挤出量一定的情况下,即挤出主电机转速不变的情况下,复合线速度越快,则复合层越薄,热熔膜温度将会下降,涂布基材上的热量减少,熔融树脂的钻合力降低,从而也就造成剥离强度的下降。相反,复合线速度降低,复合层厚度增加,复合强度也会有所提高,但却会影响生产速度。因此,在生产过程中一定要根据实际情况控制好适当的生产速度,既要保证生产进度,又要保证挤出剥离强度和复合质量。
8、挤出涂复层厚度对剥离强度的影响。在挤出复合中,挤出的熔融膜主要起热粘合作用,如果挤出涂复层的厚度太薄,热量和强度都不够,就会造成剥离强度的下降,一般要求涂复层的厚度控制在 18一20μm以上。
9、收卷张力对剥离强度的影响。收卷张力可以适当地大一些,也就是说收卷时应当尽量卷紧一点儿,这样可以避免因复合膜起皱和分层剥离而引起的粘接牢度下降。由于在收卷时被复合在一起,两种材料还未立即产生很强的粘合力,复合牢度不太好,些时适当地加大收卷张力可以使收卷平整紧凑,不容易产生收缩,经冷却定型后,复合牢度就会好一些。
10、设备工装对剥离强度的影响。
在日常生产中还应当注意对工装设备的保养和维护,保证设备处于良好的运行状态,这是保证挤出复合生产顺利进行的基本条件。还要经常检查硅橡胶压辊表面有无影响正常生产的划道、凹坑、碰伤等异常现象,一旦发现要及时修补或者更换。此外,还要注意保持各工装的清洁十净,及时清除粘附在表面上的灰尘、杂物或油污,还要经常检查硅橡胶压辊表面有无影响正常生产的划道、凹坑、碰伤等异常现象,以免影响复合产品的剥离强度。
五、底涂剂(AC制)
对剥离强度的影响在挤出复合工艺过程中,为了增强粘性,可以先在基材上涂布底涂剂,然后再用聚乙烯、聚丙烯等树脂等与之复合。涂布了底涂剂之后,可以大大提高挤出的热熔树脂同被涂布基材之间的热粘结牢度,从而提高挤出复合膜的剥离强度。
1、正确选用底涂剂(AC剂)。挤出复合用底涂剂的种类和牌号比较多,大体可分为含水型和溶剂型两大类。含水型底涂剂有聚乙烯亚胺类底涂剂,溶剂型底涂剂有钦系底涂剂、异氰酸酯系底涂剂等。含水型底涂剂一般用于被包装物不含水,复合强度要求不高的材料,而溶剂型底涂剂一般则用于被包装物含水分量较大,复合强度要求较高的材料。因此,应当根据实际情况选用合适的底涂剂,保证挤出复合产品的质量。
2、底涂的涂布量及涂布状况对剥离强度的影响。除了正确选择底涂剂之外,还必须正确调配底涂剂的粘度,保证其对被涂布基材的良好润湿,并使之有适当的涂布量,并保证足够的剥离强度。一般来说,底涂剂的涂布量在0.1—0.5g/m2(干固量)之间。此外,还必须保证底涂剂涂布的均匀性,保证熔融树脂同被涂布基材之间黏接力的均匀一致,从而使挤出复合膜的剥离强度保持恒定。
3、底涂剂的质量对剥离强度的影响。底涂剂也有一定的保存和使用期限,如果底涂剂已经超出了使用期限,或者在使用期限内就已经发生了变质,势必会影响到其作用的发挥,从而影响挤出复合膜的剥离强度。
4、底涂剂的干燥状态对剥离强度的影响。如果底涂剂干燥不充分,就会残留部分溶剂或水,从而影响挤出复合膜的粘接牢度,造成剥离强度的降低。因此,当发现底涂剂干燥不良时,应当适当地降低复合线速度,同时还可以提高干燥温度和通风量,保证底涂剂能够充分干燥。
六、车间内环境卫生
对剥离强度的影响车间内的环境卫生对挤出复合产品质量也有一定的影响,如果环境卫生状态比较差,空气中有大量的灰尘、杂质等粒子,这些粒子就会吸附到基材表面,或者落到冷却钢辊、硅橡胶压辊以及各导向辊等上面,这都会影响复合时熔融树脂膜同基材贴合的密切程度,使复合膜中夹杂异物,影响复合膜的剥离强度。因此,一定要注意使车间内的环境保持清洁、卫生。
七、结束语
前面我们对挤出复合膜剥离强度的一些主要影响因素进行了简单的分析和介绍,针对上述情况,在实际生产中我们还应当注意以下事项:
1、加强对各种原辅材料(包括薄膜、油墨、树脂、底涂剂等)的质量检测工作,严格把关,为提高复合膜质量奠定基础。
2、根据包装内容物的性质以及复合膜质量要求选用适当的底涂剂,控制好涂布量和干燥温度,使底涂剂能够充分干燥,保证复合质量。
3、在实际生产中,应当根据树脂、基材、设备等具体情况来调整和控制挤出复合工艺参数,保证复合膜的产品质量。在挤出复合生产前,一定要充分了解和掌握所用树脂的性能和各项主要指标,并以此为依据来调整生产工艺和温度,尤其是要严格控制挤出机各工作段的挤出温度,保证树脂均匀塑化,定量地从机头挤出,并能够同基材很好地粘合在一起。
4、重视设备、工装的维护和保养,保证生产过程的连续性和止常性,减少故障发生率,提高产品质量,保证优质、高产、低消耗。
5、注意保持库房和车间内的环境卫生,保证清洁干净,并应具备良好的通风条件,避免灰尘、砂粒等杂质异物对复合工艺及复合强度的影响。模切刀 压痕条 刀版弹垫 补底纸 胶条 海绵条 补底纸 压痕模 压痕线
挤出复合工艺具有投资少、成本低、生产效率高、操作简便等多方面的优点,因此,它在塑料薄膜的复合加工中占有相当重要的地位。但是,在实际生产中也难免会出现这样或那样的问题。本文,就以最为常见的剥离强度差为例与大家共同进行分析探讨。
一、薄膜基材对剥离强度的影响
1、基材表面处理效果对剥离强度的影响。被涂布基材应当预先进行电晕处理,电晕处理后的表面张力应当达到40达因以上,这样可以改进基材同熔融挤出树脂的粘结性,从而提高挤出复合强度。因此,在生产前要检测基材的表面张力是否达到要求,一发现表面张力太低,应立即更换基材或对基材重新进行表面处理。此外,经表面处理过的薄膜,其表面张力应当是均匀一致的,否则也会对剥离强度产生一定的影响,造成剥离强度不均匀、不一致的问题。
2、基材表面清洁度对剥离强度的影响。被涂布基材表面应当清洁、干净,无灰尘、无油污,如果基材表面不太清洁,粘附了灰尘、油脂等污物,就会直接影响到熔融树脂跟塑料薄膜表面的粘合力,从而使挤出复合膜的粘接强度下降。
3、其它因素的影响。对于一些易吸湿的薄膜材料(比如尼龙薄膜),如果已经发生吸湿现象,这也会影响挤出复合膜的粘接牢度。因此,对于易吸湿的薄膜材料一定要注意防潮,尼龙薄膜在使用前和使用后应当及时用铝箔将其包裹好。
二、油墨对剥离强度的影响
1、油墨质量对剥离强度的影响。
在实际生产过程中,有时候会出现无油墨或油墨较少部位的剥离强度好、而有油墨或油墨较多部位的粘合牢度反而比较差的现象,这就是由于所用的印刷油墨的适性不好,油墨与基材之间的粘接不良,从而造成挤出复合膜的剥离强度差。一旦发生这种情况,应当及时更换合适的油墨,并同油墨厂商联系,共同协商和研究解决办法。
2、油墨干燥性对剥离强度的影响。如果油墨干燥不良,特别是当油墨中大量地使用了甲苯、丁醇等沸点比较高的溶剂,而且干燥箱温度设置
不当的话,就会有少量或较大量的溶剂残留在油墨层中,复合后可能会造成复合膜的分层,使剥离强度变差。因此,在印刷过程中一定要对油墨的干燥性能进行严格的控制,保证油墨能够充分干燥。
此外,在印刷过程中还要注意对印刷速度和干燥温度等工艺条件的控制,因为它们也会对油墨中溶剂的挥发速度产生一定的影响。如果印刷速度较快,且印刷机干燥箱的温度又比较低的话,油墨中的溶剂可能无法完全挥发掉,这些残留的溶剂就会在薄膜上形成一些小泡,使复合膜粘接牢度下降。一般来说,在设定干燥箱的温度时,必须要综合考虑印刷速度、油墨的干燥速度、承印物材料的种类以及印刷图像的大小等因素。
三、挤出复合用树脂对剥离强度的影响
1、树脂类型对剥离强度的影响。挤出涂布复合用树脂可以是聚乙烯、聚丙烯、EVA、Surlyn、 Nucler、Bynel、EVAL、EAA、EMAM等。挤出涂布复合的目的不同,选用的树脂也不同。例如,用于普通层复合塑料制袋用的,可以采用热封性较好的各种热封用树脂;用于夹心挤复用的树脂,要求同面层和内封层塑料层均有良好的相容性的,可根据面层及内封层材料的不同选用各种相容剂树脂,如 Surlyn、Nucler、Bynelr等。如果树脂选用不当,会影响到它同被涂布基材的相容性,从而影响到挤出复合强度。
2、树脂熔融指数(MI)对剥离强度的影响。熔融指数(MI)是指树脂熔融料在一定温度和一定压力下,在lOmin内通过标准毛细管的重量值,以克/1Omin表示。熔融指数(MI)是树脂流动性的一种指标,一般来说,树脂的熔融指数(MI)越高,则其流动性越好,熔融薄膜的粘度越低,粘合力越大。在挤出复合工艺中,不宜选用熔融指数(MI)太小的树脂。如果树脂的熔融指数(MI)偏小,其分子量较大,则融合性比较差,不能与被涂布基材很好地粘合,致使剥离牢度有所下降。比如在使用LDPE树脂进行挤出复合时,一般选用熔融指数(MI)在4--7g/1Omin的LDPE树脂。
3、树脂密度对剥离强度的影响。树脂的密度越小,支链含量越高,表面越容易被活化,粘合力就越大,对剥离强度的提高也就越有利。
4、树脂中助剂及水分含量对剥离强度的影响。树脂中的助剂,特别是润滑剂对挤出复合膜的剥离强度有着很大的影响,比如在使用LDPE树脂进行挤出复合时,应当选用不含或少含润滑剂的挤出涂覆级树脂粒子,例如北京燕山石化公司的1C7A、上海金山石化公司的1C8A等树脂。此外,如果树脂中所含的水分比较多的话,在挤出复合过程中可能会发生塑化不良现象,从而影响复合膜的剥离强度。
四、挤出复合工艺对剥离强度的影响
1、挤出机温度对剥离强度的影响。挤出机机筒温度和T模温度的控制极为重要,是挤出复合工艺的关键和核心。温度太低,树脂塑化不良,从模口流延下来不能很好地与基材复合,致使剥离牢度下降;温度高,流出的熔薄膜氧化越充分,表面产生极性分子,对基材的亲和力越大,剥离强度也就越高。但是温度也不宜过高,否则树脂容易分解,还可能会烫伤基材,而且还会产生烟雾,污染工作环境。一般来说,挤出机机筒的温度通常控制在150℃一340℃之间,T模的温度通常控制在310℃--340'C左右,这还要根据挤出复合设备和所用树脂的具体情况来设定。
2、树脂温度对剥离强度的影响。树脂温度高,有利于熔融塑料膜在被涂布基材上的润湿和渗透,因而有利于复合强度的提高,但过高会引起分解,一般不超过350℃。如果树脂与基材压着时的温度过低,树脂表面氧化不充分,应当适当提高树脂温度。
3、气隙对剥离强度的影响。气隙是指从挤出模口到复合冷却钢辊、压力辊接触线之间的距离。由于气隙的存在,热熔膜表面会同空气中的氧气发生氧化作用,氧化后的热熔膜被涂布塑料薄膜复合时的剥离牢度会大大提高。气隙的大小对挤出剥离强度也有很大的影响,气隙太小,树脂表面氧化不充分,致使挤出复合强度变差;气隙大,热熔膜同空气接触的时间长,热熔膜表面被空气中氧气氧化的程度越厉害。增加极性基因,树脂同基材表面的黏结力也就越大,从而有利于复合强度的提高。但如果气隙太大,则热熔膜的热损失过大,温度会降低得过多,在复合时的温度过低,反而会引起剥离强度的下降,而且热封性也变差。因此,挤出复合时应当根据实际情况来调节气隙的大小,一般来说,气隙控制在 50mm—l00mm之间为宜。
4、复合压力对剥离强度的影响。复合压力小,熔融树脂与基材之间贴合不紧密,会使剥离牢度下降。但复合压力也不可太大,否则基材容易被压变形。
5、冷却钢辊表面温度对剥离强度的影响。冷却辊采用的是表面镀铬的钢辊筒,其作用是将熔融树脂薄膜的热量带走,让粘合后的复合膜立即冷却、固化,以形成较强的内聚力,使熔融薄膜跟被涂布基材粘牢、定型,不产生相对位移,从而保证良好的剥离强度。因此,冷却钢辊表面的温度对挤出复合薄膜的剥离强度有着一定的影响。如果冷却钢辊的表面温度太高,则冷却定型效果不好,可能使挤出复合膜起皱,会使复合牢度下降;但如果冷却钢辊的表面温度太低,冷却速度太快的话,也会引起复合强度的降低。一般来说,冷却辊的表面温度控制在30'C左右最佳。而且,冷却辊表面必须光滑,表面温度分布应当均匀一致,这样才能保证挤出复合膜的冷却效果一致,从而保证其粘接牢度和剥离强度的一致性。
6、硅橡胶压力辊表面状态对剥离强度的影响。硅橡胶压力辊的作用是将基材和熔融树脂膜以一定的压力压向冷却辊,使基材和熔融膜压紧、粘合,并冷却、固化成型。硅橡胶压力辊是在钢辊的外表面包覆了20—25mm厚的硅橡胶而制成的,硅橡胶的硬度一般为80--85肖氏硬度为最佳,而且,硅橡胶压力辊表面的硬度应当均匀一致,这样才能保证整体压力基本保持均匀一致,从而保证挤出复合产品剥离牢度的均匀、恒定。
7、复合线速度对剥离强度的影响。在挤出量一定的情况下,即挤出主电机转速不变的情况下,复合线速度越快,则复合层越薄,热熔膜温度将会下降,涂布基材上的热量减少,熔融树脂的钻合力降低,从而也就造成剥离强度的下降。相反,复合线速度降低,复合层厚度增加,复合强度也会有所提高,但却会影响生产速度。因此,在生产过程中一定要根据实际情况控制好适当的生产速度,既要保证生产进度,又要保证挤出剥离强度和复合质量。
8、挤出涂复层厚度对剥离强度的影响。在挤出复合中,挤出的熔融膜主要起热粘合作用,如果挤出涂复层的厚度太薄,热量和强度都不够,就会造成剥离强度的下降,一般要求涂复层的厚度控制在 18一20μm以上。
9、收卷张力对剥离强度的影响。收卷张力可以适当地大一些,也就是说收卷时应当尽量卷紧一点儿,这样可以避免因复合膜起皱和分层剥离而引起的粘接牢度下降。由于在收卷时被复合在一起,两种材料还未立即产生很强的粘合力,复合牢度不太好,些时适当地加大收卷张力可以使收卷平整紧凑,不容易产生收缩,经冷却定型后,复合牢度就会好一些。
10、设备工装对剥离强度的影响。
在日常生产中还应当注意对工装设备的保养和维护,保证设备处于良好的运行状态,这是保证挤出复合生产顺利进行的基本条件。还要经常检查硅橡胶压辊表面有无影响正常生产的划道、凹坑、碰伤等异常现象,一旦发现要及时修补或者更换。此外,还要注意保持各工装的清洁十净,及时清除粘附在表面上的灰尘、杂物或油污,还要经常检查硅橡胶压辊表面有无影响正常生产的划道、凹坑、碰伤等异常现象,以免影响复合产品的剥离强度。
五、底涂剂(AC制)
对剥离强度的影响在挤出复合工艺过程中,为了增强粘性,可以先在基材上涂布底涂剂,然后再用聚乙烯、聚丙烯等树脂等与之复合。涂布了底涂剂之后,可以大大提高挤出的热熔树脂同被涂布基材之间的热粘结牢度,从而提高挤出复合膜的剥离强度。
1、正确选用底涂剂(AC剂)。挤出复合用底涂剂的种类和牌号比较多,大体可分为含水型和溶剂型两大类。含水型底涂剂有聚乙烯亚胺类底涂剂,溶剂型底涂剂有钦系底涂剂、异氰酸酯系底涂剂等。含水型底涂剂一般用于被包装物不含水,复合强度要求不高的材料,而溶剂型底涂剂一般则用于被包装物含水分量较大,复合强度要求较高的材料。因此,应当根据实际情况选用合适的底涂剂,保证挤出复合产品的质量。
2、底涂的涂布量及涂布状况对剥离强度的影响。除了正确选择底涂剂之外,还必须正确调配底涂剂的粘度,保证其对被涂布基材的良好润湿,并使之有适当的涂布量,并保证足够的剥离强度。一般来说,底涂剂的涂布量在0.1—0.5g/m2(干固量)之间。此外,还必须保证底涂剂涂布的均匀性,保证熔融树脂同被涂布基材之间黏接力的均匀一致,从而使挤出复合膜的剥离强度保持恒定。
3、底涂剂的质量对剥离强度的影响。底涂剂也有一定的保存和使用期限,如果底涂剂已经超出了使用期限,或者在使用期限内就已经发生了变质,势必会影响到其作用的发挥,从而影响挤出复合膜的剥离强度。
4、底涂剂的干燥状态对剥离强度的影响。如果底涂剂干燥不充分,就会残留部分溶剂或水,从而影响挤出复合膜的粘接牢度,造成剥离强度的降低。因此,当发现底涂剂干燥不良时,应当适当地降低复合线速度,同时还可以提高干燥温度和通风量,保证底涂剂能够充分干燥。
六、车间内环境卫生
对剥离强度的影响车间内的环境卫生对挤出复合产品质量也有一定的影响,如果环境卫生状态比较差,空气中有大量的灰尘、杂质等粒子,这些粒子就会吸附到基材表面,或者落到冷却钢辊、硅橡胶压辊以及各导向辊等上面,这都会影响复合时熔融树脂膜同基材贴合的密切程度,使复合膜中夹杂异物,影响复合膜的剥离强度。因此,一定要注意使车间内的环境保持清洁、卫生。
七、结束语
前面我们对挤出复合膜剥离强度的一些主要影响因素进行了简单的分析和介绍,针对上述情况,在实际生产中我们还应当注意以下事项:
1、加强对各种原辅材料(包括薄膜、油墨、树脂、底涂剂等)的质量检测工作,严格把关,为提高复合膜质量奠定基础。
2、根据包装内容物的性质以及复合膜质量要求选用适当的底涂剂,控制好涂布量和干燥温度,使底涂剂能够充分干燥,保证复合质量。
3、在实际生产中,应当根据树脂、基材、设备等具体情况来调整和控制挤出复合工艺参数,保证复合膜的产品质量。在挤出复合生产前,一定要充分了解和掌握所用树脂的性能和各项主要指标,并以此为依据来调整生产工艺和温度,尤其是要严格控制挤出机各工作段的挤出温度,保证树脂均匀塑化,定量地从机头挤出,并能够同基材很好地粘合在一起。
4、重视设备、工装的维护和保养,保证生产过程的连续性和止常性,减少故障发生率,提高产品质量,保证优质、高产、低消耗。
5、注意保持库房和车间内的环境卫生,保证清洁干净,并应具备良好的通风条件,避免灰尘、砂粒等杂质异物对复合工艺及复合强度的影响。模切刀 压痕条 刀版弹垫 补底纸 胶条 海绵条 补底纸 压痕模 压痕线
下一篇:丝网印花的挖剪法制版上一篇:如何选择适宜的不干胶标签印刷方式
相关资讯
- 纸张模切起毛的具体原因有哪些
- 模切纸张起毛可更换模切刀或是防爆胶条可解
- 刀模制作整个步骤第一次分享
- 刀模的正确保养方法
- 怎样选择优质的垫刀泡棉
- 刀版弹垫的弹性强度与硬度的关系,提升工作
- 纸板切不穿是和选用的刀版弹垫有关系吗
- 刀版弹垫的选用方法
- 防止瓦楞纸张模切爆边用的防爆胶条
- 模切散纸乱纸用什么样的海绵条比较合适
- 海绵条是否能够解决纸张模切起毛散纸乱纸问
- 刀模垫是什么有什么作用
- 刀模海绵条有什么作用又如何使用
- eva泡棉有哪些特点和实际用途
- 什么样的刀模弹垫质量比较好
- 第一次发现EVA泡棉居然有这么多用途
- 刀模粘贴刀模弹垫太厚会造成哪些严重后果
- 优质的垫刀泡棉都有哪些特征
- eva内衬包装大特性有哪些
- 使用eva内衬包装的产品有哪些优势
- 压痕线规格选用公式详解
- 反压线选用介绍
- 防爆胶条使用方法
- 什么是刀版弹垫?
- 浅析轮转胶印机印刷张力的调节与控制
- 卡纸模切时选择压痕线型号规则
- 印刷材料DULEE反压痕线详细
- 模切刀常用规格
- 刀模板上的刀是如何装入的
- 日本中山迷利镜面刀介绍
- 刀版弹垫胶条起到什么作用?
- 模切彩盒有误差是什么原因?
- EVA泡绵包装材料特性
- 泡绵XPE是什么呢?
- 模具材料模切刀规格描述
- 模切压痕工艺常见技术问题
- 如何处理模切压痕加工中的出现的故障?三
- 如何处理模切压痕加工中的出现的故障?二
- 如何处理模切压痕加工中的出现的故障?一
- 模切刀模要如何选用压痕线
您的浏览历史