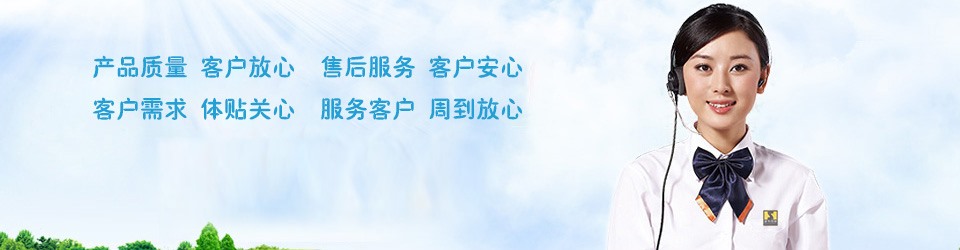
解决“粘合不良” 提高瓦楞纸板质量
发布时间:06-30 作者:小华 来源:深华印材 查看: 次
在瓦楞纸箱的生产实践中,各种纸张间的粘合是非常重要的一个环节,并且在相当程度上决定了产品的质量水平。各层纸页之间粘合是否紧密牢固,直接影响瓦楞纸板的质量。粘合良好的瓦楞纸板表面平整,不起泡、无褶皱、不翘曲,加工成瓦楞纸箱后纸页之间不会产生分离,外观硬挺,有较好的抗压和缓冲性能,能有效地保护内装商品免受外界不利因素影响而受损。但是,在瓦楞纸板生产线上出现瓦楞纸板粘合不良(起泡、脱胶、假粒)的现象时有发生。据了解,瓦楞纸板生产线产生的废次品中,因粘合问题造成的占了近七成。所以,要真正达到降本增效的目的,必须将因粘和问题产生的废品率控制在合适范围内。接下来,我们将找出纸板“粘合不良”产生的原因,为您在实际生产中遇到问题时,提供一系列解决方案。
瓦楞纸板是否粘合良好是对瓦楞纸板进行物理性能检验的一个重要指标。影响瓦楞纸板粘合强度的原因比较复杂,概括地讲,原纸、黏合剂、瓦楞纸板机械、生产计划安排和员工操作水平等等,均对其施加了影响,并且以上因素之间还相互影响。
原纸
在此主要表现在几个方面:
1. 原纸的含水率:箱板纸或瓦楞原纸过于干燥(低于6%)或水分过大(高于12%),都会造成瓦楞纸板粘合不佳。太干燥时,黏合剂的膨润和粘合所必需的水分被原纸吸收,结果造成胶未糊化现象。水分过大时,多余的水分对热量的吸收,导致热量不足,从而粘合不佳。解决方案是严格控制原纸的水分,太干燥时须喷湿处理,水分过大时,须适当增加原纸的水分,预热面积,如果仍旧不佳,则必须换纸。
2. 原纸的吸水性或透水性的好坏:原纸的材质、紧度和施胶度,决定了其吸水性或透水性。吸水性或透水性太差的原纸,会抑制黏合剂的渗透粘合;吸水性或透水性太强的原纸,一会造成胶未糊化现象,二会产生透胶现象。前一种的解决方案是黏合剂中使用了添加剂,利用添加剂改善原纸表面的疏水性质,使黏合剂得以渗透。此外,适当增加黏合剂涂布量也是必要的。我们知道,瓦楞纸板的粘合首先是楞纸楞峰涂胶,然后与面里纸或夹芯的结合,黏合剂在任一层面间的转移受到阻碍,都将影响粘合效果。例如,德州沪平永发造纸A公司的A 级草浆瓦楞纸,经过重施胶处理,吸水性差,不使用耐水型黏合剂无法得到良好的粘合。后一种的解决方案是适当增加黏合剂粘度。
3. 原纸的裂断长:它是原纸张强度与定量的比率,表示一定宽度的纸条被自身重量拉断时所需的长度。如果原纸裂断长较低,那么在瓦线速度达到一定程度时,势必造成经常断纸和停机,此时停留在烘道中的瓦楞纸板吸收过多的热量,再好的黏合剂也无法得到良好的粘合。这种情况,解决办法是降低机速,或提高原纸质量,把裂断长纳入原纸检验项目。
4. 原纸一边松懈:如果是瓦楞纸一边松,会造成高低不平瓦楞,影响与纸板的贴合;如果是纸板一边松,则会在纸板表面形成折皱。严重时均形成粘合不佳。解决办法惟有更换原纸。
黏合剂的质量
此处主要反映在两方面 :一是淀粉质量的好坏,二是黏合剂制作工艺优劣。
1. 淀粉的等级较低,意味着加工精细度差,蛋白质、脂肪和灰份等杂质较多,使用这样的淀粉,一是将消耗更多的氢氧化钠,使黏合剂不稳定,粘合的瓦楞纸板易吸潮,在潮湿环境下短时间放置,会使瓦楞纸板脱胶 ;二是黏合剂易以较大的淀粉颗粒和杂质为核心产生凝胶,使黏合剂流动性变差,涂布不均,使瓦楞纸板局部无胶、少胶,产生粘合不佳。解决办法是使用高质量的淀粉,若是玉米淀粉,宜采用工业一级品以上。黏合剂制作工艺优劣显得更加重要。瓦楞纸板的黏合剂,有适当的固体含量、粘度以及必要的糊化温度。一般的黏合剂在循环使用中,其粘度每通过循环泵一次,就有降低的趋势。此时,应加入新制备的黏合剂混合使用。
2. 此外,在假日停机时,多余的黏合剂贮存于贮罐内,特别是炎热夏季,细菌将淀粉分解,发生腐败现象而使粘度急剧下降,产生淀粉沉淀,造成粘合不良。解决办法是在黏合剂制备时加入防腐剂,如甲醛,每200kg淀粉配0.35l,或五氯酚钠,每200kg淀粉配0.32kg。
3. 当制作耐水纸板时,往往会使用高级板纸和瓦楞纸,配合使用的是耐水型黏合剂。这种黏合剂中一般加有热塑性树脂的聚合和缩合仍能进行,有时粘度急剧上升,已不适合瓦楞纸板机的使用条件。解决办法是重新调整胶量,使粘度达到使用要求。
4. 当面里纸甚至夹芯纸的定量合紧度较高时(定量180g/m2以上,紧度0.70g/m3以上),有时因热量不足引起粘合不良。由于定量较高的面纸厚度较大,紧度较高的面纸材质致密,影响了热传递,而A瓦楞热传递需要较多的时间,结果导致单面A瓦楞与夹芯纸之间发生粘合不良。这种情况的解决方案是降低机速,同时加大厚纸与预热器的包角。
5. 假如瓦楞纸板机的绝对热量不足时,使用糊化温度低的黏合剂也是一个好办法。面纸定量较低时(低于180g/m2),容易在面纸表面产生泡状现象,称为“水泡”,这是一种局部脱胶现象。在双面瓦楞纸板机上或将纸板装在小车上经过较短时间,便在纸板单面上发生这种现象,情况主要是挂面纸板水份较大或瓦楞纸板过于干燥造成的。由于热和水份的不平衡,过于干燥的瓦楞纸板在双面瓦楞纸板机出口处吸潮,因纵向已被固定,所以横向伸长,表面形成小泡状。解决方案除了尽量减少黏合剂用量,切断热盘的一部分热或提高机速,制作高固含低粘度的黏合剂也是一个办法,但是一定要掌握好糊化温度。
瓦楞纸板机机械因素
瓦楞纸板机机械方面的因素主要是 :核心部件瓦楞辊的精度、硬度和磨损程度 ;瓦楞纸板粘合装置的先进性;热部的构造 ;是否采用全自动接纸装置等等。
1. 瓦楞辊 :瓦楞辊常被比喻为瓦楞纸板机的心脏,可见其位置举足轻重。
1) 用新瓦楞辊生产的瓦楞纸板发生局部粘合不良,其重要的一个原因就是瓦楞辊精度不高。解决方案是选用高精度瓦楞辊,制成的瓦楞在一个横幅上高度差很小,涂布较少的黏合剂就能达到理想的粘合效果。
2) 普通的瓦楞辊表面镀铬以增加硬度,由于中低档瓦楞纸有一定的含砂量,砂子的主要成份是二氧化硅,它的硬度仅次于金刚石,所以对普通的瓦楞辊表面镀铬磨损较为剧烈。一般的纸箱企业生产的瓦楞纸板规格种类较多,例如使用幅宽2200mm的瓦线,规格可能从1200mm到2200mm,种类高中低档均有,加上长期在中部走纸,短短几个月,就可能使瓦楞辊的中高丧失。这种情况下生产的瓦楞纸板,中部粘合不良甚至没有粘合。为了使中部得到理想的粘合,不得不增加压力辊压力,但是这只是权宜之计,时间不长,这种情况更加严重,压力辊压力加大至板纸两端被瓦楞辊咬破,仍旧无法获得粘合。这种情况的解决方案,除了避免使用含砂量高的瓦楞原纸,将小规格整合成大规格 (必要时统一用料,合理搭配生产),更换新瓦楞辊尤其使用喷涂碳化钨替代镀铬瓦楞辊是最有效的 (但成本较高,须结合业务情况统筹考虑) 。镀铬瓦楞辊使用寿命为2000万米,整修次数最多3次且外径逐次递减。喷涂碳化钨瓦楞辊使用寿命增加一倍,且楞型和本体不受损坏,外径不减少。省纸、强度高也是其优势。
2. 瓦楞纸板贴合装置 :经过涂胶的单面瓦楞纸板与板纸的贴合,一般是通过压力辊 (又称骑轮)加压实现的。由于长期与纸张摩擦,也会产生磨损,造成整个横幅贴合不一致,进而使瓦楞纸板局部粘合不良,多见于两端。解决方案 :增加压力,使两端的粘合改观,但中部瓦楞可能被压变形 ;在压力辊两端辊面上贴胶带纸,也能使粘合改善,但难以控制,可能使两端瓦楞变形 ;采用触压棒代替压力辊,是最好的选择。
触压棒是由一组载有弹簧、长宽约12.2cm×8.8cm的压片所组成,工作时无须再借助其他动力,平行且预留适当缝隙,安装于贴合机糊轮上端,在纸板接触面上,触压棒压板特别设计与糊轮相同的弧度,使压力稳定,黏合剂涂布均匀。每个触压片上有独立控制的弹簧,自动调整不规则跳动,防止压扁楞型。热板部用热压片替代重力辊,使瓦楞纸板各层之间得到充分贴合,也能大大改善粘合质量。
3. 热部的构造:普通的瓦线,热部的加热、加压机构是由固定式的热板和重力压力装置构成的,所以其热传递是一个定值。生产中,一般是根据原纸的等级、定量、厚度,通过调整蒸汽压力来控制热板温度的。生产过程中,当出现原纸拉力不足(主要表现在裂断长不够,前面已述及)、缺材 (会造成应力集中)、接头、断头等情况时,常会发生断纸,造成减速续接 (除非有全自动接纸装置) 甚至停机,机速的改变打破了热传递的平衡,固定的热板又无法调整热量,结果使烘道中的瓦楞纸受热过度,造成脱胶、翘曲等现象。此时的解决方案只能通过提升帆布带装置使瓦楞纸脱离热板 (停机超过40秒必须提升帆布带装置),尽管脱胶、翘曲等现象大为改观,但是仍然不能避免局部脱胶现象,且伴随纸板表面出现折痕,影响外观,并对印刷工序造成一定困难。如果热板设计成液压机提升可变热量的加热系统,生产中通过调整热板倾斜度,使热板与瓦楞纸之间产生一定的空隙,部分热量从空隙散出,从而减少热板向瓦楞纸板传递的热量,达到热传递的平衡。或者在热板间隙处设计安装窄小的喷管,用一组空气调节阀门,在机速降低时开启调节阀门,使吹入热板与瓦楞纸板之间的空气扩散,形成一个刚好能把瓦楞纸和帆布带装置从热板上托起的薄片状空气膜,达到减少热板向瓦楞纸板过多热传递的目的。
4. 全自动接纸装置 :使用全自动接纸装置避免了减速和停机,从而保证自使至终热量的稳定传递。
生产计划安排和员工操作水平
1. 一般的纸箱企业,由于生产的瓦楞纸板规格和用料五花八门,这就涉及生产计划安排。
1) 生产中若做完小规格立即换做大规格,大规格瓦楞纸板的两端往往会出现粘合不良。主要原因是:由于在中部走纸,做完小规格瓦楞纸板后,热板中部与两端相比,温度较低,换做大规格瓦楞纸板后,可能两端的黏合剂已经糊化,而两端的黏合剂糊化太过,结果是两端脱胶。而且,根据热胀冷缩的原理,由于在中部走纸,热板中部的膨胀程度不及热板两端,从热板横向看,已经不再是平面,而是曲面,瓦楞纸与热板之间的粘合,在整个横向上不一致,造成吸收的热量也有差别,黏合剂的糊化程度也不一样,结果出现粘合不佳。解决方案是:在生产计划安排时,尽可能先生产大规格瓦楞纸,使各种瓦楞纸板都受热均匀,糊化一致。如果由于客户催货,无法实现以上计划安排,那么在从小规格换成大规格瓦楞纸板前,应至少停机半小时,使热板上的热量重新分布。
2) 在从一种类型的瓦楞纸板换成另一种类型的瓦楞纸板时,如不同种类对黏合剂的要求不一样。解决方案是:优化瓦楞纸板组合,将原纸的种类从几十种压缩成几种,小规格瓦楞纸板配套成大规格瓦楞纸板。
3) 统计表明,瓦楞纸板线产生废次品的主要原因是换纸造成的,这其中又有约70%是粘合不良。原因是换纸时机速的改变或停机。解决方案是:除了压缩原纸种类,适当提高原纸等级,用低定量高强度原纸代替高定量低强度原纸,适当提高原纸等级,用低定量强度原纸代替高定量低强度原纸。当批量较大时,这种方法效果显著。因为同等重量的一卷筒原纸,定量越低,米数越长,不但减少了库存和运输费用,而且使用时换纸的次数也减少了。
2. 员工操作水平也是一个重要因素。
1) 有时候,生产的瓦楞纸板在粘接处形成有规则的无糊料白线,或全面粘合不良。前者原因是:瓦楞纸张力过大或水份过多,或者导纸板在胶槽中陷入,导致在导纸板位置无黏合剂涂上楞顶。解决方案:调整瓦楞纸张力和水份,适当增加黏合剂涂布量,调整导纸板。 2) 全面粘合不良的原因:黏合剂质量不高,或胶槽内黏合剂不足,涂布量太少;黏合剂糊化温度太高,或获取的温度过少使粘接处的黏合剂不能糊化;或者是温度太高黏合剂分子结构遭到破坏,失去粘合性质;或者是上胶辊离瓦楞顶面间隙大以及原纸吸收性不好等等。解决方案:若是黏合剂质量不高,则须提高质量;若是胶槽内黏合剂不足,则应增加槽内黏合剂量,达到适当的涂布量;若是黏合剂糊化温度太高,则应调整制胶配方,适当增加氢氧化钠用量以降低糊化温度。若是单面瓦楞纸板全面粘合不良,则有可能是未及时排放冷凝水。瓦楞辊筒内的热蒸汽释放热量后变成冷凝水,若不及时排放,则会吸收蒸汽的一部分热量而使瓦楞辊表面温度不够,引起全面的粘合不良。解决方案是密切关注单面瓦楞纸板粘合情况,及时排放冷凝水。同理,若是双面瓦楞纸板全面粘合不良,也可能是热板处未及时排放冷凝水,解决方案同上;
3) 大多数情况是换纸或停机造成的,原因是:换纸太慢,停机时间太长。解决方案:换纸熟练,要求在40秒内完成;停机时间不能超过1分钟,否则须提升帆布装置。若是上胶辊瓦楞顶面间隙大,则须加以调整。若是原纸吸收性不好,则须更换吸收性合适的原纸。
综上所述,解决瓦楞纸板粘接不良问题,不仅需对纸板的粘接、成型原理有较深入的认识,还需对纸板生产设备的运作特性有较深入的研究,从而达到以最佳的工艺方案实现最理想的产品质量,使纸板生产线高速、高效、高质量的运作起来。模切刀 压痕条 刀版弹垫 补底纸 胶条 海绵条 补底纸 压痕模 压痕线
瓦楞纸板是否粘合良好是对瓦楞纸板进行物理性能检验的一个重要指标。影响瓦楞纸板粘合强度的原因比较复杂,概括地讲,原纸、黏合剂、瓦楞纸板机械、生产计划安排和员工操作水平等等,均对其施加了影响,并且以上因素之间还相互影响。
原纸
在此主要表现在几个方面:
1. 原纸的含水率:箱板纸或瓦楞原纸过于干燥(低于6%)或水分过大(高于12%),都会造成瓦楞纸板粘合不佳。太干燥时,黏合剂的膨润和粘合所必需的水分被原纸吸收,结果造成胶未糊化现象。水分过大时,多余的水分对热量的吸收,导致热量不足,从而粘合不佳。解决方案是严格控制原纸的水分,太干燥时须喷湿处理,水分过大时,须适当增加原纸的水分,预热面积,如果仍旧不佳,则必须换纸。
2. 原纸的吸水性或透水性的好坏:原纸的材质、紧度和施胶度,决定了其吸水性或透水性。吸水性或透水性太差的原纸,会抑制黏合剂的渗透粘合;吸水性或透水性太强的原纸,一会造成胶未糊化现象,二会产生透胶现象。前一种的解决方案是黏合剂中使用了添加剂,利用添加剂改善原纸表面的疏水性质,使黏合剂得以渗透。此外,适当增加黏合剂涂布量也是必要的。我们知道,瓦楞纸板的粘合首先是楞纸楞峰涂胶,然后与面里纸或夹芯的结合,黏合剂在任一层面间的转移受到阻碍,都将影响粘合效果。例如,德州沪平永发造纸A公司的A 级草浆瓦楞纸,经过重施胶处理,吸水性差,不使用耐水型黏合剂无法得到良好的粘合。后一种的解决方案是适当增加黏合剂粘度。
3. 原纸的裂断长:它是原纸张强度与定量的比率,表示一定宽度的纸条被自身重量拉断时所需的长度。如果原纸裂断长较低,那么在瓦线速度达到一定程度时,势必造成经常断纸和停机,此时停留在烘道中的瓦楞纸板吸收过多的热量,再好的黏合剂也无法得到良好的粘合。这种情况,解决办法是降低机速,或提高原纸质量,把裂断长纳入原纸检验项目。
4. 原纸一边松懈:如果是瓦楞纸一边松,会造成高低不平瓦楞,影响与纸板的贴合;如果是纸板一边松,则会在纸板表面形成折皱。严重时均形成粘合不佳。解决办法惟有更换原纸。
黏合剂的质量
此处主要反映在两方面 :一是淀粉质量的好坏,二是黏合剂制作工艺优劣。
1. 淀粉的等级较低,意味着加工精细度差,蛋白质、脂肪和灰份等杂质较多,使用这样的淀粉,一是将消耗更多的氢氧化钠,使黏合剂不稳定,粘合的瓦楞纸板易吸潮,在潮湿环境下短时间放置,会使瓦楞纸板脱胶 ;二是黏合剂易以较大的淀粉颗粒和杂质为核心产生凝胶,使黏合剂流动性变差,涂布不均,使瓦楞纸板局部无胶、少胶,产生粘合不佳。解决办法是使用高质量的淀粉,若是玉米淀粉,宜采用工业一级品以上。黏合剂制作工艺优劣显得更加重要。瓦楞纸板的黏合剂,有适当的固体含量、粘度以及必要的糊化温度。一般的黏合剂在循环使用中,其粘度每通过循环泵一次,就有降低的趋势。此时,应加入新制备的黏合剂混合使用。
2. 此外,在假日停机时,多余的黏合剂贮存于贮罐内,特别是炎热夏季,细菌将淀粉分解,发生腐败现象而使粘度急剧下降,产生淀粉沉淀,造成粘合不良。解决办法是在黏合剂制备时加入防腐剂,如甲醛,每200kg淀粉配0.35l,或五氯酚钠,每200kg淀粉配0.32kg。
3. 当制作耐水纸板时,往往会使用高级板纸和瓦楞纸,配合使用的是耐水型黏合剂。这种黏合剂中一般加有热塑性树脂的聚合和缩合仍能进行,有时粘度急剧上升,已不适合瓦楞纸板机的使用条件。解决办法是重新调整胶量,使粘度达到使用要求。
4. 当面里纸甚至夹芯纸的定量合紧度较高时(定量180g/m2以上,紧度0.70g/m3以上),有时因热量不足引起粘合不良。由于定量较高的面纸厚度较大,紧度较高的面纸材质致密,影响了热传递,而A瓦楞热传递需要较多的时间,结果导致单面A瓦楞与夹芯纸之间发生粘合不良。这种情况的解决方案是降低机速,同时加大厚纸与预热器的包角。
5. 假如瓦楞纸板机的绝对热量不足时,使用糊化温度低的黏合剂也是一个好办法。面纸定量较低时(低于180g/m2),容易在面纸表面产生泡状现象,称为“水泡”,这是一种局部脱胶现象。在双面瓦楞纸板机上或将纸板装在小车上经过较短时间,便在纸板单面上发生这种现象,情况主要是挂面纸板水份较大或瓦楞纸板过于干燥造成的。由于热和水份的不平衡,过于干燥的瓦楞纸板在双面瓦楞纸板机出口处吸潮,因纵向已被固定,所以横向伸长,表面形成小泡状。解决方案除了尽量减少黏合剂用量,切断热盘的一部分热或提高机速,制作高固含低粘度的黏合剂也是一个办法,但是一定要掌握好糊化温度。
瓦楞纸板机机械因素
瓦楞纸板机机械方面的因素主要是 :核心部件瓦楞辊的精度、硬度和磨损程度 ;瓦楞纸板粘合装置的先进性;热部的构造 ;是否采用全自动接纸装置等等。
1. 瓦楞辊 :瓦楞辊常被比喻为瓦楞纸板机的心脏,可见其位置举足轻重。
1) 用新瓦楞辊生产的瓦楞纸板发生局部粘合不良,其重要的一个原因就是瓦楞辊精度不高。解决方案是选用高精度瓦楞辊,制成的瓦楞在一个横幅上高度差很小,涂布较少的黏合剂就能达到理想的粘合效果。
2) 普通的瓦楞辊表面镀铬以增加硬度,由于中低档瓦楞纸有一定的含砂量,砂子的主要成份是二氧化硅,它的硬度仅次于金刚石,所以对普通的瓦楞辊表面镀铬磨损较为剧烈。一般的纸箱企业生产的瓦楞纸板规格种类较多,例如使用幅宽2200mm的瓦线,规格可能从1200mm到2200mm,种类高中低档均有,加上长期在中部走纸,短短几个月,就可能使瓦楞辊的中高丧失。这种情况下生产的瓦楞纸板,中部粘合不良甚至没有粘合。为了使中部得到理想的粘合,不得不增加压力辊压力,但是这只是权宜之计,时间不长,这种情况更加严重,压力辊压力加大至板纸两端被瓦楞辊咬破,仍旧无法获得粘合。这种情况的解决方案,除了避免使用含砂量高的瓦楞原纸,将小规格整合成大规格 (必要时统一用料,合理搭配生产),更换新瓦楞辊尤其使用喷涂碳化钨替代镀铬瓦楞辊是最有效的 (但成本较高,须结合业务情况统筹考虑) 。镀铬瓦楞辊使用寿命为2000万米,整修次数最多3次且外径逐次递减。喷涂碳化钨瓦楞辊使用寿命增加一倍,且楞型和本体不受损坏,外径不减少。省纸、强度高也是其优势。
2. 瓦楞纸板贴合装置 :经过涂胶的单面瓦楞纸板与板纸的贴合,一般是通过压力辊 (又称骑轮)加压实现的。由于长期与纸张摩擦,也会产生磨损,造成整个横幅贴合不一致,进而使瓦楞纸板局部粘合不良,多见于两端。解决方案 :增加压力,使两端的粘合改观,但中部瓦楞可能被压变形 ;在压力辊两端辊面上贴胶带纸,也能使粘合改善,但难以控制,可能使两端瓦楞变形 ;采用触压棒代替压力辊,是最好的选择。
触压棒是由一组载有弹簧、长宽约12.2cm×8.8cm的压片所组成,工作时无须再借助其他动力,平行且预留适当缝隙,安装于贴合机糊轮上端,在纸板接触面上,触压棒压板特别设计与糊轮相同的弧度,使压力稳定,黏合剂涂布均匀。每个触压片上有独立控制的弹簧,自动调整不规则跳动,防止压扁楞型。热板部用热压片替代重力辊,使瓦楞纸板各层之间得到充分贴合,也能大大改善粘合质量。
3. 热部的构造:普通的瓦线,热部的加热、加压机构是由固定式的热板和重力压力装置构成的,所以其热传递是一个定值。生产中,一般是根据原纸的等级、定量、厚度,通过调整蒸汽压力来控制热板温度的。生产过程中,当出现原纸拉力不足(主要表现在裂断长不够,前面已述及)、缺材 (会造成应力集中)、接头、断头等情况时,常会发生断纸,造成减速续接 (除非有全自动接纸装置) 甚至停机,机速的改变打破了热传递的平衡,固定的热板又无法调整热量,结果使烘道中的瓦楞纸受热过度,造成脱胶、翘曲等现象。此时的解决方案只能通过提升帆布带装置使瓦楞纸脱离热板 (停机超过40秒必须提升帆布带装置),尽管脱胶、翘曲等现象大为改观,但是仍然不能避免局部脱胶现象,且伴随纸板表面出现折痕,影响外观,并对印刷工序造成一定困难。如果热板设计成液压机提升可变热量的加热系统,生产中通过调整热板倾斜度,使热板与瓦楞纸之间产生一定的空隙,部分热量从空隙散出,从而减少热板向瓦楞纸板传递的热量,达到热传递的平衡。或者在热板间隙处设计安装窄小的喷管,用一组空气调节阀门,在机速降低时开启调节阀门,使吹入热板与瓦楞纸板之间的空气扩散,形成一个刚好能把瓦楞纸和帆布带装置从热板上托起的薄片状空气膜,达到减少热板向瓦楞纸板过多热传递的目的。
4. 全自动接纸装置 :使用全自动接纸装置避免了减速和停机,从而保证自使至终热量的稳定传递。
生产计划安排和员工操作水平
1. 一般的纸箱企业,由于生产的瓦楞纸板规格和用料五花八门,这就涉及生产计划安排。
1) 生产中若做完小规格立即换做大规格,大规格瓦楞纸板的两端往往会出现粘合不良。主要原因是:由于在中部走纸,做完小规格瓦楞纸板后,热板中部与两端相比,温度较低,换做大规格瓦楞纸板后,可能两端的黏合剂已经糊化,而两端的黏合剂糊化太过,结果是两端脱胶。而且,根据热胀冷缩的原理,由于在中部走纸,热板中部的膨胀程度不及热板两端,从热板横向看,已经不再是平面,而是曲面,瓦楞纸与热板之间的粘合,在整个横向上不一致,造成吸收的热量也有差别,黏合剂的糊化程度也不一样,结果出现粘合不佳。解决方案是:在生产计划安排时,尽可能先生产大规格瓦楞纸,使各种瓦楞纸板都受热均匀,糊化一致。如果由于客户催货,无法实现以上计划安排,那么在从小规格换成大规格瓦楞纸板前,应至少停机半小时,使热板上的热量重新分布。
2) 在从一种类型的瓦楞纸板换成另一种类型的瓦楞纸板时,如不同种类对黏合剂的要求不一样。解决方案是:优化瓦楞纸板组合,将原纸的种类从几十种压缩成几种,小规格瓦楞纸板配套成大规格瓦楞纸板。
3) 统计表明,瓦楞纸板线产生废次品的主要原因是换纸造成的,这其中又有约70%是粘合不良。原因是换纸时机速的改变或停机。解决方案是:除了压缩原纸种类,适当提高原纸等级,用低定量高强度原纸代替高定量低强度原纸,适当提高原纸等级,用低定量强度原纸代替高定量低强度原纸。当批量较大时,这种方法效果显著。因为同等重量的一卷筒原纸,定量越低,米数越长,不但减少了库存和运输费用,而且使用时换纸的次数也减少了。
2. 员工操作水平也是一个重要因素。
1) 有时候,生产的瓦楞纸板在粘接处形成有规则的无糊料白线,或全面粘合不良。前者原因是:瓦楞纸张力过大或水份过多,或者导纸板在胶槽中陷入,导致在导纸板位置无黏合剂涂上楞顶。解决方案:调整瓦楞纸张力和水份,适当增加黏合剂涂布量,调整导纸板。 2) 全面粘合不良的原因:黏合剂质量不高,或胶槽内黏合剂不足,涂布量太少;黏合剂糊化温度太高,或获取的温度过少使粘接处的黏合剂不能糊化;或者是温度太高黏合剂分子结构遭到破坏,失去粘合性质;或者是上胶辊离瓦楞顶面间隙大以及原纸吸收性不好等等。解决方案:若是黏合剂质量不高,则须提高质量;若是胶槽内黏合剂不足,则应增加槽内黏合剂量,达到适当的涂布量;若是黏合剂糊化温度太高,则应调整制胶配方,适当增加氢氧化钠用量以降低糊化温度。若是单面瓦楞纸板全面粘合不良,则有可能是未及时排放冷凝水。瓦楞辊筒内的热蒸汽释放热量后变成冷凝水,若不及时排放,则会吸收蒸汽的一部分热量而使瓦楞辊表面温度不够,引起全面的粘合不良。解决方案是密切关注单面瓦楞纸板粘合情况,及时排放冷凝水。同理,若是双面瓦楞纸板全面粘合不良,也可能是热板处未及时排放冷凝水,解决方案同上;
3) 大多数情况是换纸或停机造成的,原因是:换纸太慢,停机时间太长。解决方案:换纸熟练,要求在40秒内完成;停机时间不能超过1分钟,否则须提升帆布装置。若是上胶辊瓦楞顶面间隙大,则须加以调整。若是原纸吸收性不好,则须更换吸收性合适的原纸。
综上所述,解决瓦楞纸板粘接不良问题,不仅需对纸板的粘接、成型原理有较深入的认识,还需对纸板生产设备的运作特性有较深入的研究,从而达到以最佳的工艺方案实现最理想的产品质量,使纸板生产线高速、高效、高质量的运作起来。模切刀 压痕条 刀版弹垫 补底纸 胶条 海绵条 补底纸 压痕模 压痕线
下一篇:名片印刷制作所需设备以及耗材选用上一篇:非吸收性UV印刷油墨的应用
相关资讯
- 彩盒包装加工有些切不穿是什么原因用补底钢
- 手动模切机怎样选用刀模海棉条
- 刀版弹垫正确安装使用能避免卡纸彩盒模切起
- 刀版弹垫这样选择也能避免纸张模切起毛问题
- 彩盒包装纸箱模切起毛拉丝?防爆胶条来帮您
- 解决刀版弹垫太硬纸板啤不穿的问题
- 模切2200g的灰板纸用哪种硬度的刀版弹垫?
- 刀版弹垫在纸箱包装模切中起到哪些作用
- 刀版弹垫在彩盒包装模切中主要起到什么作用
- 刀版弹垫的硬度在彩盒包装模切成型时有什么
- 压痕线不规则会造成哪些模切问题
- 手动啤机用的刀版弹垫自动模切机用的有哪些
- 怎样快速区分垫刀泡棉的质量
- 刀模夹缝胶条使用方法和作用
- 印刷包装刀模为什么要贴垫刀泡棉
- 印刷包装刀模先贴刀版弹垫还是先装压痕条
- 刀版弹垫的选择需要注意哪些方面
- 导致压痕线条移位的因素有哪些?
- 印刷包装模切过程中刀模用的垫刀泡棉起什么
- 有哪些因素可能导致压痕条在模切时偏移
- 压痕线规格选用公式详解
- 反压线选用介绍
- 防爆胶条使用方法
- 刀模板上的刀是如何装入的
- 什么是刀版弹垫?
- 浅析轮转胶印机印刷张力的调节与控制
- 卡纸模切时选择压痕线型号规则
- 印刷材料DULEE反压痕线详细
- 模切刀模要如何选用压痕线
- 模切刀常用规格
- 刀版弹垫胶条起到什么作用?
- 模切彩盒有误差是什么原因?
- EVA泡绵包装材料特性
- 泡绵XPE是什么呢?
- 模具材料模切刀规格描述
- 模切压痕工艺常见技术问题
- 如何处理模切压痕加工中的出现的故障?三
- 如何处理模切压痕加工中的出现的故障?二
- 如何处理模切压痕加工中的出现的故障?一
- 模切刀模要如何选用压痕线
您的浏览历史